[ad_1]
In a sense, land speed races are all about power. The faster you run, the more force you need to overcome air resistance. Therefore, the more power you have, the faster you can go with the right gear. Or you can cut air resistance and go faster with the same power. Most racers put effort into both.
Matt Brown is an automotive engineer. Autopian Contributor and YouTuber behind the channel SuperfastMatt. As you can guess from his name, he likes to run fast and is working on his homebrew land speed racer to make it faster than ever. To do this, he decided to design an aerodynamic body to fit his previously bare frame.

Matt begins by outlining the basic elements that influence design. The car needs space for him inside, along with wheels, windshield, exhaust, etc. He needs to create a streamlined body that is as slippery and aerodynamic as possible, while still allowing for the basic functionality of the vehicle.
This video describes a common method for designing a streamlined vehicle with a rounded nose and tapered body toward the rear. In fact, smooth air return at the rear of the vehicle is just as important, if not more so, than very carefully drilling holes at the front of the vehicle.
In contrast, Matt’s ground speed car is nothing like that. It’s now an exposed frame with protrusions from various components sticking out here and there, all of which contribute to some pretty bad drag numbers.
To design the streamliner body, Matt decided to use a tool called AirShaper, and the company is sponsoring the build. AirShaper is a tool for computational fluid dynamics analysis (HECFD for short). Essentially, it allows you to digitally simulate the flow of air or water over an object, and is often more convenient than building scale models and using wind tunnels. Performing a meaningful he CFD analysis requires a high degree of skill, and typically requires a high degree of knowledge and experience to perform properly. If done poorly, the results of the calculations will have little correlation to what happens in the real world.
The point of AirShaper is to make CFD more accessible than traditional packages, which can require a very steep learning curve. Having taken an introductory CFD course in college, I understand its value. Matt was also particularly lucky to have AirShaper CEO Wouter Lemery on hand to offer his insight into the design.
Oh, and before we get into that, here’s a crash course in aerodynamics. There are two types of drag that he is primarily concerned with.There is pressure resistancealso known as form drag, this is caused by the shape of the object. It all has to do with pressure fluctuations across the vehicle. Imagine a sphere moving through the air. You will see that the air is compressed as it hits the front of the sphere. On the other hand, when air flows around the sphere, a boundary layer forms and then separates towards the rear. This leaves a turbulent “wake” behind the sphere where the low pressure zone is located. This pressure difference creates a drag force that pushes the sphere back. after that, Frictional resistanceThis is much easier. It depends on the friction of air molecules on the surface of the vehicle.
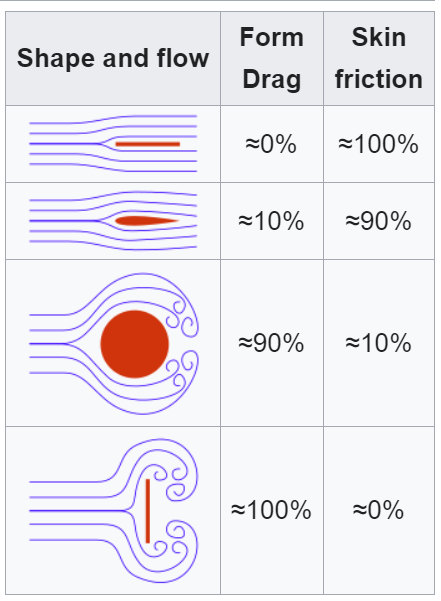
Matt previously drove the car on the Bonneville Salt Flats without bodies and used the results there as validation for the numbers coming from the Air Shaper. According to CFD analysis, the coefficient of drag (Cd) of his bare frame design was worse than his 18-wheeler, at 0.825. Land high-speed vehicles have a much smaller frontal area, so the total drag on the vehicle is much lower, which essentially means the vehicle is less aerodynamically efficient than a semi-truck.
Matt also pointed out that the car was a bit unstable from his experience on the salt flats. Air Shapers similarly pointed out that there are no aerodynamic forces to help maintain a straight line, which is undesirable for land-speed cars. In fact, the car was so unstable that it reached a top speed of 157 miles per hour according to the dashboard and then rolled back, although I doubt it could actually reach closer to 180 miles per hour without the bodywork. . AirShaper only considers aerodynamic drag and suggests that this car could reach speeds of 180 mph with just 130 horsepower. Matt had the car’s dyno tested at 195 horsepower, and considering the rolling resistance on sticky salt and the loss of horsepower due to altitude at Bonneville, he thinks his analysis was about right.
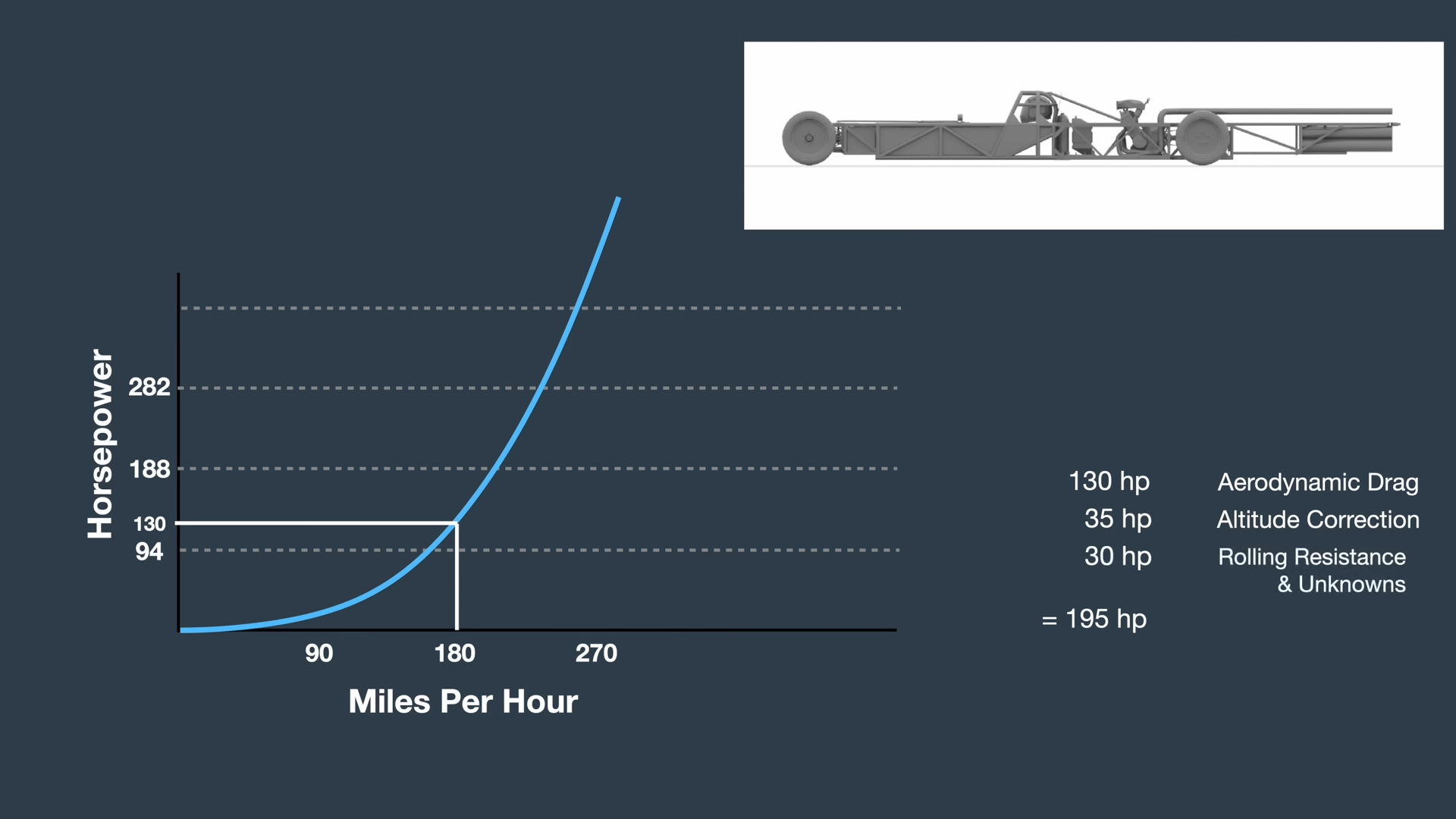
When designing the body, Matt started by keeping things as simple as possible. He first sketched out a design that was rounded at the front and tapered to the rear, leaving room for the driver, engine, and wheels. He pointed out that the car’s width is 22 inches to accommodate the front and rear wheels, and there is little benefit to slimming down the area between the front and rear wheels. This allowed him to form the main part of the lower body from three flat panels, making the task of building the body easier. He’s considering doing that, or bending large pieces of plastic into a single U-shaped panel to place under the car.
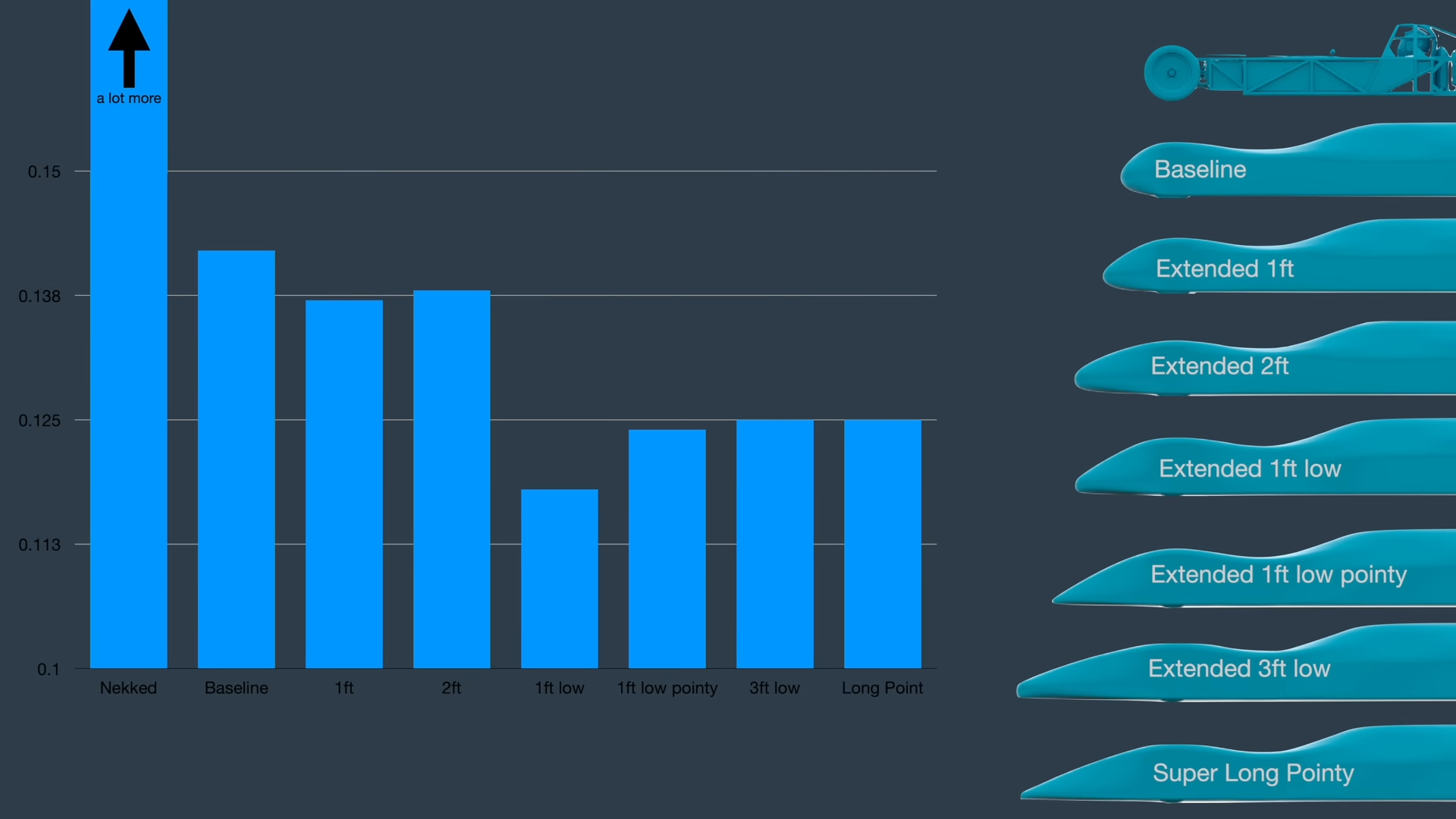
Matt then got down to business and optimized the nose to minimize drag coefficient. He set up his AirShaper to simulate a vehicle moving along the ground. This configures his CFD analysis with the correct parameters for the interaction between the ground and the vehicle itself. AirShaper analysis continued to find that a longer, lower nose reduces drag. However, if it’s too long or too pointy, it won’t be of much use. He now has to figure out how to create a gap between the front wheels to improve visibility without compromising drag.
At the rear, Matt experimented with changing the angle at which the tail tapers. He realized that a longer, smoother tail would be worse for his own basic design. This is because the more subtle taper angle reduces pressure drag by mixing air more gently, while the larger surface area of this design further increases frictional drag. He eventually shortened his basic design until he found a point where the resistance stopped improving.
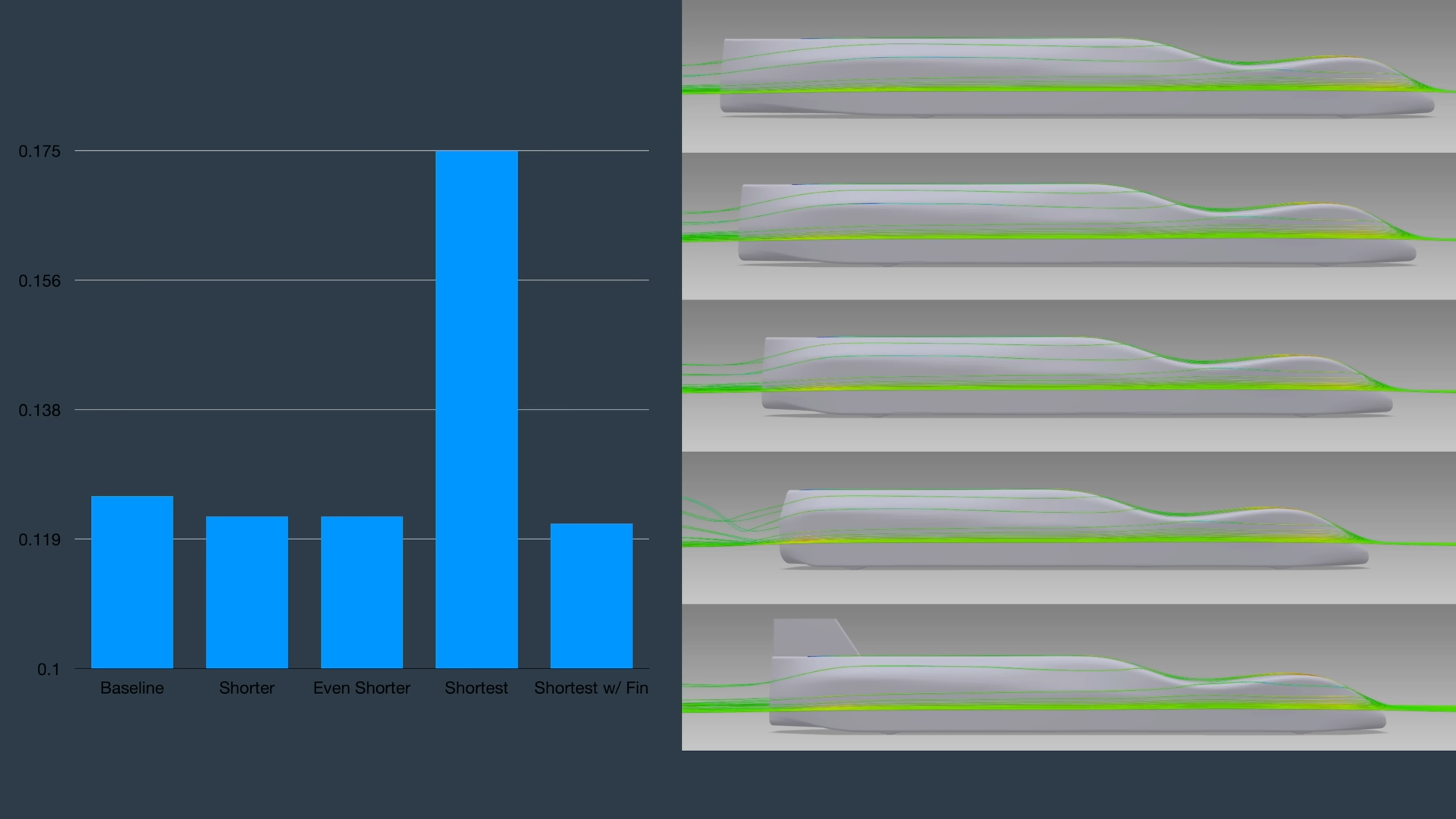
When it came to stability, Matt wanted the car to stay straight and narrow. This meant ensuring that the center of pressure was behind the car’s center of gravity. Basically, think of the center of gravity as the point of balance on which the mass of an object acts. The center of pressure is the point at which the total pressure field on the car acts.
Finding the center of pressure is complicated, but basically, increasing the resistance at the rear of the car will pull the car backwards. Matt accomplished this by adding a fin to the rear of the car. This is the same principle as the fletching on the back of an arrow or the flight on the back of a dart. Moves the center of pressure aft, behind the center of gravity, providing aerodynamic stability during operation.
Adding fins adds some drag due to the increased frontal area. However, by making it much smaller and having a streamlined teardrop shape, we minimize the additional drag in both frictional and pressure drag.
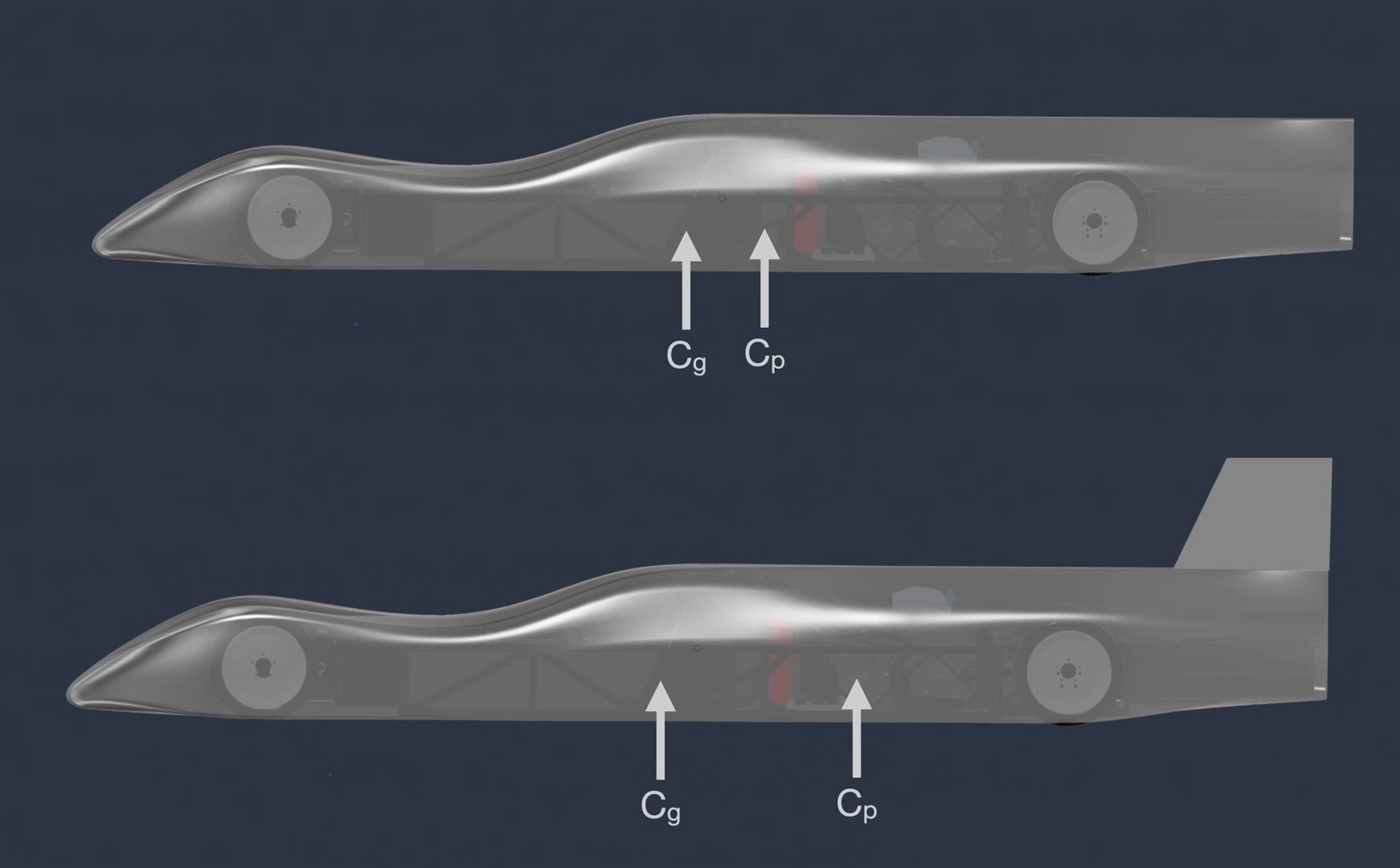
Matt then put together a rough estimate of the car’s top speed based on rolling resistance and altitude loss similar to our previous bare frame run at Bonneville. He thinks that even though he runs this car on two cylinders instead of four, it will be much faster than his last run with the streamlined body. He estimates that the top speed in this configuration is 265 miles per hour. At full power, as in the previous race, he calculates a top speed of 325 mph.
All these numbers are very rough. They are based on a number of assumptions and well-supported extrapolations. However, it does give you a vague idea of how much of an impact a streamliner body can have. Sure, the top speed has increased significantly, but that’s what you get when you reduce Cd from 0.825 to 0.12.
Construction comes with several challenges. Matt has to find a way to build most of the design out of fiberglass. In addition, practical considerations such as cutouts for fasteners, wheels, etc. compromise efficiency. But regardless, we should expect Matt to go even faster when he returns to the salt with a new streamlined body of his own design. I can’t wait to see how the real-world results compare to the simulations.
Image credit: Superfast Matt (via YouTube screenshot), drag diagram credit to BoH, CC BY-SA 3.0
[ad_2]
Source link